eSubsea perform Solidworks Simulation Studies on all types of subsea structures, parts and components using the advanced but easy-to-use finite element analysis program and analysis tool SolidWorks Simulation by Dassault Systems. Parts or assemblies created in the 3D CAD program SolidWorks can be imported, refined, meshed and analysis using FEA.
FEA During Product Development
These services and analyses are particular useful during product development and product innovation for smaller mechanical parts and beam structures where the beams are short and local effects are of importance to the stress results. The structural integrity can be monitored as part of the 3D CAD modelling process and hence the design is optimised continuously.

However, as for any computer analysis program, the output is only as correct as the input. eSubsea has the experience to generate correct input as loads and boundary conditions and to evaluate and verify that the finite element analysis results are as expected.
eSubsea can either received your 3D CAD part or assembly model ready for analysis or make it ourself based on your design input.
Finite Element Analysis Studies
The following types of structural analysis or studies can be done fast track using Simulation:
- Linear Static Analysis
- Non-linear Analysis
- Pressure Vessel Studies
- Frequency Studies
- Buckling Studies
- Fatigue Studies
- Thermal Studies
- Motion Analysis
The results from these analyses and studies will quickly give accurate stress, displacement and strain plots to evaluate if the design has the structural capacity for the loads applied.
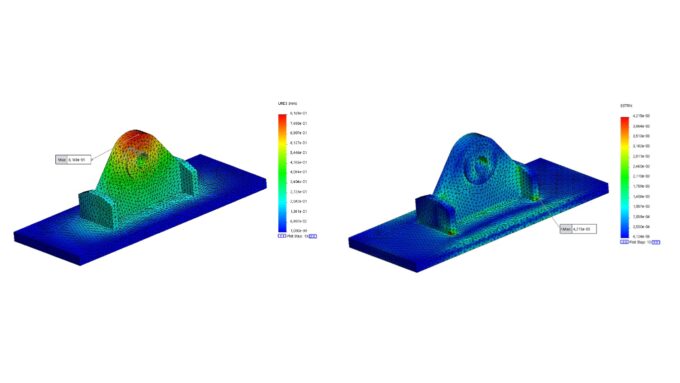
The finite element analysis do not perform code checks and hence it is often required to run another structural analysis and perform code check to verify that the FEA results are code compliant.
